Hardie Board Replacement Cost A Comprehensive Guide
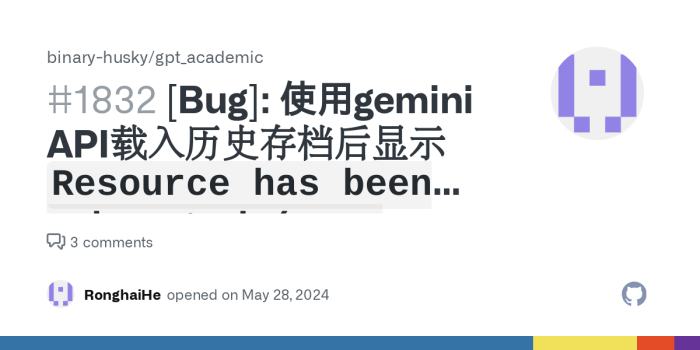
Hardie board replacement cost is a significant factor when considering home exterior renovations. This guide breaks down the costs involved, from material selection and labor expenses to permits and potential hidden costs. We’ll explore different Hardie board types, compare them to alternatives like vinyl and wood, and offer advice on finding reputable contractors. Ultimately, understanding these factors empowers you to make informed decisions and budget effectively for your project.
We’ll cover everything from estimating material costs and labor expenses to navigating the process of finding and hiring qualified contractors. We’ll also delve into the long-term cost benefits and drawbacks of Hardie board compared to other siding options, helping you weigh the pros and cons before making a final decision. Get ready to learn how to manage your Hardie board replacement project with confidence and clarity.
Factors Affecting Hardie Board Replacement Cost
Replacing Hardie board siding isn’t a one-size-fits-all project; the cost varies significantly based on several interconnected factors. Understanding these factors will help you budget accurately and avoid unexpected expenses. This section breaks down the key variables influencing the final price.
Labor Costs and Geographic Location
Labor costs are a substantial portion of the total expense. These costs fluctuate widely depending on your geographic location. Highly populated urban areas with a high demand for skilled labor tend to have higher hourly rates for contractors compared to more rural regions. The cost of living, prevailing wage laws, and the overall competitiveness of the local construction market all play a significant role. For example, a contractor in New York City will likely charge more per hour than one in a smaller town in the Midwest. This difference can substantially impact the overall project cost, even if the materials remain the same.
Hardie Board Type and Quality, Hardie board replacement cost
Hardie board comes in various types, each with a different price point. Lap siding is a common choice, known for its clean lines and relatively straightforward installation. Shingles, on the other hand, offer a more textured, traditional look, but their complex installation can increase labor costs. Beyond the basic type, the quality and thickness of the board also matter. Thicker boards are more durable and weather-resistant but cost more. The specific color or finish you choose can also impact the price, with some custom colors or finishes adding a premium.
Project Size and Complexity
The size of your house and the complexity of the replacement project significantly affect the overall cost. A small project involving the replacement of a few damaged panels will naturally be cheaper than a full-house siding replacement. Complexity factors include the presence of intricate architectural details, such as dormers, bay windows, or multiple rooflines. These features require more precise cutting and fitting, increasing both labor time and material waste, ultimately driving up the cost. A house with simple, flat siding will be less expensive to re-side than one with numerous architectural embellishments.
Cost Comparison Table
The following table provides estimated costs for different Hardie board types, assuming a 100 sq ft area. Remember that these are averages and can vary based on the factors discussed above.
Board Type | Average Cost per Square Foot | Installation Cost per Square Foot | Total Estimated Cost (100 sq ft) |
---|---|---|---|
Lap Siding | $3 – $5 | $4 – $7 | $700 – $1200 |
Shingles | $4 – $6 | $6 – $9 | $1000 – $1500 |
Vertical Siding | $3.50 – $5.50 | $5 – $8 | $850 – $1350 |
Panel Siding | $2.50 – $4.50 | $3 – $6 | $550 – $1050 |
Estimating Hardie Board Replacement Costs
Accurately estimating the cost of replacing Hardie board siding is crucial for budgeting and planning your home improvement project. This involves more than just the price of the materials; it requires a comprehensive understanding of labor costs, permits, and potential hidden expenses. Let’s break down how to create a realistic budget.
Material Cost Calculation
Calculating material costs begins with accurately measuring the area needing replacement. This typically involves measuring the length and height of each section of siding, accounting for windows, doors, and other openings. Next, you’ll need to determine the quantity of Hardie board panels required. Remember to add extra for cuts and potential waste (typically 5-10%). Consult your local home improvement store or supplier for current pricing per panel or square foot. Don’t forget to factor in the cost of nails, screws, caulk, primer, paint or stain, and any underlayment or flashing that might be necessary. A detailed list of materials with quantities and prices will form the foundation of your material cost estimate. For example, if you need 100 square feet of Hardie board at $2.50 per square foot, the material cost alone would be $250.
Labor Cost Estimation
Estimating labor costs depends heavily on the project’s complexity and scope. A small, straightforward replacement might only require a day or two of labor, while a large, complex project could take weeks. You can obtain labor cost estimates in a few ways: Get quotes from multiple contractors, use online cost calculators (be aware these are estimates), or consult industry averages for your region. These averages are usually expressed as a cost per square foot or per hour. Remember to consider factors like the height of the house, accessibility, and any necessary scaffolding. For instance, if a contractor charges $50 per hour and estimates the job will take 20 hours, the labor cost would be $1000.
Sample Cost Breakdown
Let’s illustrate with a sample cost breakdown for a typical 200 square foot Hardie board replacement project:
Item | Quantity | Cost per Unit | Total Cost |
---|---|---|---|
Hardie Board | 220 sq ft (10% extra) | $2.50/sq ft | $550 |
Nails/Fasteners | 1 box | $20 | $20 |
Caulk | 1 tube | $15 | $15 |
Primer | 1 gallon | $30 | $30 |
Paint | 2 gallons | $40/gallon | $80 |
Labor | 20 hours | $50/hour | $1000 |
Permits | 1 | $100 | $100 |
Total Estimated Cost | $1800 |
Permit and Associated Fees
Building permits are often required for exterior home renovations, including Hardie board replacement. Check with your local building department to determine permit requirements and associated fees. These fees vary widely by location and project scope. Other associated fees might include dumpster rental for waste disposal, and potentially, fees for inspections. Always budget for these upfront to avoid unexpected costs.
Potential Hidden Costs
It’s crucial to anticipate potential hidden costs that can significantly impact your budget.
- Unexpected damage: Discovering rotted wood or insect infestation beneath the siding will add to both material and labor costs.
- Material price fluctuations: Lumber and building material prices can fluctuate; locking in prices with your supplier can mitigate this risk.
- Additional repairs: You might find other issues, like damaged flashing or trim, during the replacement process.
- Disposal fees: Proper disposal of old siding and debris can incur additional costs.
- Scaffolding rental: If your home is tall, scaffolding might be necessary, adding to your expenses.
Comparing Hardie Board to Alternative Materials: Hardie Board Replacement Cost
Choosing the right siding material for your home involves weighing initial costs against long-term expenses, maintenance needs, and environmental impact. Hardie board, vinyl, and wood are popular choices, each with its own set of advantages and disadvantages. Let’s compare them to help you make an informed decision.
Cost Comparison of Siding Materials
The initial cost of siding varies significantly depending on the material, labor costs, and the complexity of the installation. Hardie board typically sits in the mid-range, more expensive than vinyl but less costly than high-end wood siding. Vinyl siding offers the lowest upfront cost, while premium wood options, like cedar, can be significantly more expensive. However, remember that initial cost is only one piece of the puzzle.
Long-Term Cost Benefits and Drawbacks
While vinyl siding boasts a low initial investment, it may require replacement sooner than Hardie board or wood, leading to higher long-term costs. Hardie board offers a good balance between initial cost and longevity. High-quality wood siding, though expensive upfront, can last for decades with proper maintenance, potentially making it a cost-effective choice in the long run. However, the cost of that maintenance needs to be factored in.
Maintenance Requirements and Lifespan
Vinyl siding generally requires minimal maintenance, primarily involving occasional cleaning. Hardie board is relatively low-maintenance but may need repainting every 10-15 years depending on the climate and exposure to the elements. Wood siding demands the most upkeep, including regular painting or staining, caulking, and potential repairs to address rot or insect damage. Lifespans also vary greatly: vinyl siding might last 20-30 years, Hardie board 30-50 years, and well-maintained wood siding can potentially last 50 years or more.
Environmental Impact of Siding Materials
The environmental impact of siding materials is a complex issue. Vinyl siding is a petroleum-based product, contributing to carbon emissions during its production and disposal. Hardie board, composed of cement and cellulose fibers, has a lower carbon footprint than vinyl but still requires energy for manufacturing and transportation. Wood siding, sourced from sustainably managed forests, can be a relatively environmentally friendly option, especially if it’s locally sourced and from a renewable resource. However, the environmental impact also depends on the manufacturing processes and transportation distances involved.
Material | Initial Cost (per sq ft, estimate) | Maintenance Cost (10 years, estimate) | Lifespan (years) |
---|---|---|---|
Hardie Board | $3-$7 | $1-$3 | 30-50 |
Vinyl Siding | $1-$3 | $0.50-$1 | 20-30 |
Wood Siding (Cedar) | $5-$15 | $2-$5 | 50+ |
Finding and Hiring Contractors for Hardie Board Replacement
Finding the right contractor for your Hardie board replacement is crucial for a successful and long-lasting outcome. A poorly chosen contractor can lead to shoddy workmanship, cost overruns, and even safety hazards. Taking the time to thoroughly vet potential contractors will save you headaches and money in the long run.
Locating Qualified and Reputable Contractors
Several avenues exist for finding qualified and reputable contractors. Online directories, such as those provided by the National Association of the Remodeling Industry (NARI) or Angie’s List (now Angi), offer contractor profiles with reviews and ratings. Local home improvement stores often maintain lists of preferred contractors, and word-of-mouth referrals from trusted friends, family, or neighbors can be invaluable. Checking online review platforms like Yelp and Google My Business can also provide insights into a contractor’s reputation and customer satisfaction levels. Remember to look for contractors specializing in exterior siding replacement for optimal results.
Obtaining Multiple Bids and Comparing Proposals
Getting at least three bids from different contractors is essential. This allows for a fair comparison of pricing, proposed materials, and project timelines. Each bid should be detailed, outlining the scope of work, materials to be used (including specific Hardie board types and colors), labor costs, and a projected completion schedule. Comparing these proposals side-by-side will reveal discrepancies and help you identify the most competitive and comprehensive offer. For example, one contractor might offer a slightly higher price but include superior-grade Hardie board, potentially leading to long-term cost savings.
Key Aspects to Include in a Contractor Contract
A comprehensive contract protects both you and the contractor. It should clearly define the scope of work, including detailed descriptions of all tasks involved in the Hardie board replacement. Specific materials to be used, along with their manufacturer and model numbers, should be explicitly stated. The total cost, payment schedule (including any down payments and final payment terms), and project timeline with start and completion dates should be included. Crucially, the contract should specify the warranty offered on both the workmanship and materials used. Consider adding a clause outlining the process for handling disputes or unexpected issues.
Verifying a Contractor’s License and Insurance
Before hiring any contractor, verify their licensing and insurance coverage. Contact your local licensing board to confirm that their license is current and valid. Request proof of general liability insurance and workers’ compensation insurance. This ensures that you are protected in case of accidents or damages during the project. A contractor without proper insurance leaves you financially vulnerable in the event of an incident on your property.
Questions to Ask Potential Contractors
Before committing to a contractor, ask specific questions to assess their expertise and professionalism. Inquire about their experience with Hardie board installation, request references from previous clients, and ask for details about their project management process. Discuss their approach to handling unexpected issues or delays, and clarify their warranty policies. Confirm their understanding of local building codes and permit requirements. Finally, ask about their cleanup procedures to ensure a clean and organized worksite. By asking these questions, you can gauge their professionalism and suitability for the project.
Visual Examples of Hardie Board Replacement Projects
Seeing is believing, and when it comes to Hardie board replacement, visual examples can significantly impact your understanding of the process and the final results. This section provides scenarios illustrating both small and large-scale projects, highlighting the transformation achieved and the associated costs.
Small-Scale Hardie Board Replacement: Repairing Damaged Sections
Let’s imagine a scenario where a homeowner notices some damaged sections on their Hardie board siding due to a recent storm. Specifically, a few planks near a corner show signs of impact damage and water staining. The area affected is approximately 4 feet by 2 feet. To repair this, the homeowner needs to purchase new Hardie board planks (approximately $100), caulk ($15), and paint to match the existing siding ($50). Labor costs, assuming the homeowner hires a handyman for a half-day, could range from $200 to $300. Therefore, the total cost for this small-scale repair could fall between $365 and $465. The visual difference before and after would be a noticeable absence of the damaged planks, replaced with seamlessly integrated new material, restoring the original aesthetic.
Large-Scale Hardie Board Replacement: Full House Resurfacing
Now, consider a larger project: a complete resurfacing of a 2,000 square foot house. This requires a significant material investment. Assuming a cost of $8 per square foot for the Hardie board itself, materials alone would cost around $16,000. Additional materials like trim, fasteners, and underlayment could add another $4,000 to $6,000 to the total. Labor costs for a full house resurfacing project are substantial, potentially ranging from $10,000 to $15,000 depending on the complexity and the contractor’s rates. The total cost for this project could range from $30,000 to $36,000. The visual transformation would be dramatic. A faded, weathered, or damaged exterior would be replaced with a fresh, uniformly colored, and modern-looking façade.
Before-and-After Visual Comparison of Hardie Board Replacement
Imagine a home with aging, faded beige siding, showing signs of cracking and discoloration. This is the “before” picture. After the Hardie board replacement, the same house might be clad in a rich, deep gray. The new siding is smooth, unblemished, and creates a sleek, contemporary look. The color change alone drastically alters the home’s aesthetic appeal. Beyond color, the “after” image showcases the uniformity of the new siding, eliminating the unevenness and damage of the old. The overall impression is one of significant improvement, boosting curb appeal and property value.
Removing Old Siding Before Installing New Hardie Board
The process begins with careful removal of the old siding. This often involves using pry bars to loosen and remove individual planks, starting from the bottom and working upwards. Nails are removed, and any damaged sheathing or underlying structure is repaired. Once the old siding is completely removed, the underlying surface is inspected for any issues like rot or insect damage. These need to be addressed before the new Hardie board can be installed. This preparation step is crucial for ensuring a long-lasting and aesthetically pleasing result. A thorough cleaning follows to remove any debris or loose particles before the installation of new underlayment and Hardie board begins.
Final Summary
Replacing your Hardie board siding is a significant investment, but understanding the costs involved and making informed choices can lead to a successful and aesthetically pleasing outcome. By carefully considering factors like material selection, labor costs, and contractor selection, you can ensure a smooth renovation process and a long-lasting, beautiful exterior for your home. Remember to factor in potential hidden costs and get multiple bids to secure the best value for your money. Your dream exterior is within reach!
FAQ Section
What factors influence Hardie board’s lifespan?
Proper installation, regular maintenance (cleaning and repainting as needed), and the climate all affect Hardie board’s lifespan. Exposure to harsh weather can shorten its life.
Can I install Hardie board myself?
While possible for smaller projects, professional installation is generally recommended for larger areas or complex designs to ensure proper installation and warranty validity.
How long does a Hardie board replacement project typically take?
The project duration varies greatly depending on the size and complexity of the project. Smaller repairs might take a day or two, while a full house replacement could take several weeks.
Is there a warranty on Hardie board?
Yes, James Hardie, the manufacturer, offers warranties on their products. However, warranty coverage may depend on proper installation and maintenance. Check the manufacturer’s website for details.
What are some signs that my Hardie board needs replacing?
Look for signs of damage like cracks, water damage, significant fading, or loose boards. Also, consider the overall aesthetic appeal and if it aligns with your current home style.
Comments are closed.