How Much Is New Siding On A House?
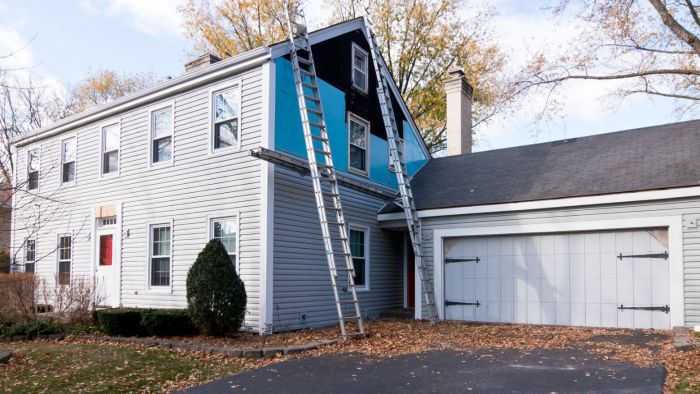
How much is new siding on a house? That’s a question many homeowners grapple with, and the answer, as you’ll soon discover, isn’t a simple number. The cost of replacing your home’s siding depends on a surprisingly large number of factors, from the type of siding you choose to your home’s size and even your location. We’ll break down all the key cost drivers, explore different siding options, and help you navigate the process of finding a reputable contractor to get the job done right. This guide will equip you with the knowledge to make informed decisions and create a realistic budget.
From understanding the intricacies of material costs (vinyl is generally cheaper than fiber cement, for example) to grasping the nuances of regional labor rates, we’ll cover it all. We’ll also help you compare different siding materials, weigh their pros and cons, and ultimately help you choose the best option for your home and budget. Get ready to dive into the world of siding replacement – and get a clearer picture of what you can expect to pay.
Cost Factors Influencing Siding Prices
Source: cloudfront.net
Getting new siding is a significant home improvement project, and understanding the cost factors is crucial for budgeting and planning. Several key elements contribute to the final price, ranging from the type of siding you choose to regional labor rates. This information will help you navigate the pricing landscape and make informed decisions.
Siding Material Costs
The type of siding you select dramatically impacts the overall cost. Different materials offer varying levels of durability, aesthetic appeal, and maintenance requirements. This directly translates to price differences.
Siding Material | Price Range Per Square Foot | Durability | Maintenance |
---|---|---|---|
Vinyl | $2-$6 | Moderate; susceptible to damage from impact | Low; typically requires occasional cleaning |
Wood | $4-$15+ | High; can last for decades with proper maintenance | High; requires regular painting, staining, and potential repairs |
Fiber Cement | $6-$15+ | Very High; highly resistant to fire, insects, and rot | Low; requires minimal maintenance, occasional cleaning |
Metal (Aluminum or Steel) | $8-$20+ | High; durable and long-lasting | Low; resistant to damage and requires minimal maintenance |
For example, a vinyl siding project might cost significantly less per square foot than one using high-end cedar wood or engineered wood siding. Fiber cement, while more expensive upfront, often boasts a longer lifespan, potentially offsetting the higher initial cost over time.
House Size and Complexity
The square footage of your home’s exterior is a major determinant of siding costs. Larger houses naturally require more materials and labor, leading to higher overall expenses. Beyond size, the complexity of your home’s architecture also plays a role. A home with numerous dormers, intricate trim work, or multiple levels will require more time and effort to side, thus increasing the cost. A simple ranch-style home will generally be less expensive to side than a Victorian-style house with many gables and decorative elements.
Regional Variations in Labor and Material Costs
Labor costs vary significantly across different regions of the country. Areas with a high cost of living or a shortage of skilled labor tend to have higher labor rates for siding installation. Material costs can also fluctuate depending on location, transportation distances, and local supply and demand. For instance, lumber prices can be significantly higher in areas with limited access to timber resources or during periods of high construction activity. Therefore, a siding project in a high-cost area like New York City will likely be more expensive than a similar project in a more rural area.
Permit Fees and Other Costs
Obtaining necessary building permits is a crucial step in any home improvement project. Permit fees vary depending on your location and the scope of the project. Other costs to consider include waste disposal, removal of old siding, and potential repairs to underlying sheathing or wall structure if discovered during the installation process. These can add a few hundred dollars or more to the total cost depending on the circumstances.
Siding Installation Process and Timeline
Getting new siding is a significant home improvement project. Understanding the process and the time it takes is crucial for planning and managing expectations. This section Artikels the typical steps involved and provides a realistic timeframe for completion. Remember, these are estimates, and your specific project may vary.
A siding installation project is a multi-stage process that requires careful planning and execution. From the initial assessment to the final cleanup, several key steps ensure a successful and long-lasting result. Proper preparation and attention to detail at each stage are critical to minimize potential issues and delays.
Siding Installation Steps
The installation process typically involves these key steps:
- Initial Consultation and Measurement: A contractor visits your home to assess the existing siding, discuss your preferences (material, color, style), and take precise measurements to determine material needs and create a detailed quote.
- Permitting and Material Acquisition: Necessary permits are obtained from your local authorities. The contractor orders the chosen siding materials, which may take some time depending on availability and supplier lead times.
- Preparation and Demolition: Existing siding is carefully removed, ensuring minimal damage to the underlying structure. Any necessary repairs to the house’s exterior are addressed at this stage, such as replacing damaged sheathing or addressing water damage.
- Installation of New Siding: This is the most labor-intensive part of the project. Workers install the new siding according to the manufacturer’s instructions and industry best practices, paying close attention to details like flashing and sealing to prevent water damage.
- Finishing Touches: This includes installing trim, caulking, and painting or staining as needed. All loose ends are carefully addressed to create a seamless and aesthetically pleasing finish.
- Final Inspection and Cleanup: A thorough inspection is conducted to ensure the work meets the agreed-upon standards. All debris and leftover materials are removed from the property, leaving your home clean and ready to enjoy your new siding.
Project Timeframes
The total time required for siding installation varies greatly depending on several factors, including the size and complexity of the house, weather conditions, and the contractor’s workload. However, you can expect the following as rough estimates:
- Small House (under 1500 sq ft): 1-2 weeks
- Medium House (1500-2500 sq ft): 2-4 weeks
- Large House (over 2500 sq ft): 4-6 weeks or more
These are just averages. A particularly complex project, such as one requiring extensive repairs or involving intricate detailing, could easily take longer.
Potential Delays and Cost Impacts
Several factors can cause delays, ultimately impacting the overall project cost. Understanding these potential delays allows for better project planning and cost management.
- Weather: Inclement weather, such as heavy rain or extreme temperatures, can significantly delay the project. This can lead to increased labor costs as the project extends beyond the initial timeline.
- Material Availability: Delays in receiving materials due to supply chain issues or backorders can disrupt the project schedule and potentially increase costs due to extended labor or storage fees.
- Unforeseen Repairs: Discovering unexpected damage during the demolition or preparation phase can add time and expense to the project. For example, finding extensive rot in the sheathing will require additional time and materials to repair before siding installation can continue.
- Contractor Availability: If the contractor is already booked or experiences unforeseen circumstances, this can cause delays. While this isn’t always predictable, choosing a reputable and well-organized contractor can help mitigate this risk.
For example, a project initially estimated at 2 weeks could easily extend to 3 or 4 weeks if unexpected rot is discovered, requiring extensive repairs to the underlying structure. This added time translates directly into higher labor costs for the contractor.
Comparing Different Siding Materials
Source: angi.com
Choosing the right siding for your home involves weighing several factors, primarily cost, longevity, maintenance, and aesthetics. This section compares four popular siding options: vinyl, wood, fiber cement, and metal, helping you make an informed decision.
Siding Material Comparison
The following table summarizes the key differences between vinyl, wood, fiber cement, and metal siding. Remember that prices can vary significantly based on location, installer, and specific product features.
Siding Material | Cost (per sq ft) | Longevity (Years) | Maintenance | Aesthetic Appeal |
---|---|---|---|---|
Vinyl | $3-$8 | 20-40 | Low; occasional cleaning | Wide variety of colors and styles; can mimic other materials |
Wood | $7-$15+ | 20-50+ (with proper maintenance) | High; regular painting, staining, and potential repairs | Classic, natural look; many styles and finishes available |
Fiber Cement | $8-$15+ | 30-50+ | Medium; occasional cleaning and repainting (every 10-15 years) | Versatile; can mimic wood, stone, or stucco |
Metal | $9-$20+ | 40-75+ | Low; occasional cleaning; resistant to damage | Modern, sleek look; durable and long-lasting |
Siding Lifespan and Maintenance Visualization
Imagine four bar graphs representing the lifespan of each siding type. The horizontal axis represents years, and the vertical axis represents the siding type.
* Vinyl: A bar reaching to 20-40 years, with a small, shaded area indicating minimal maintenance needs (occasional cleaning).
* Wood: A bar reaching potentially beyond 50 years, but significantly shorter if not maintained, with a large, shaded area indicating frequent maintenance (painting, staining, repairs).
* Fiber Cement: A bar extending to 30-50 years, with a medium-sized shaded area indicating moderate maintenance (occasional cleaning and repainting).
* Metal: The longest bar, extending to 40-75 years, with a very small shaded area indicating minimal maintenance (cleaning).
This visual representation clearly shows the relationship between lifespan and maintenance requirements for each siding type. Higher upfront costs for materials like fiber cement and metal often translate to lower long-term maintenance costs.
Energy Efficiency and Environmental Impact
Vinyl siding generally offers good insulation properties, helping to reduce energy costs. However, it’s a petroleum-based product with a significant carbon footprint during manufacturing. Wood siding, while a renewable resource, requires significant energy for processing and transportation. Furthermore, the need for regular painting or staining introduces additional environmental considerations. Fiber cement is a more sustainable choice, containing recycled materials and requiring less maintenance. Metal siding is highly durable and long-lasting, reducing the need for frequent replacements, but its production can have environmental impacts.
Finding and Vetting Contractors: How Much Is New Siding On A House
Finding the right contractor for your siding project is crucial for a successful outcome. A poorly chosen contractor can lead to shoddy workmanship, cost overruns, and lengthy delays. This section will guide you through the process of finding and vetting reputable siding contractors in your area, ensuring you make an informed decision.
Finding qualified siding contractors involves a multi-step process that goes beyond simply searching online. Thorough vetting is essential to protect your investment and avoid potential problems down the line. Remember, the time you spend upfront will save you headaches and money later.
Contractor Search Strategies
Begin your search by leveraging multiple resources to broaden your reach and increase your chances of finding suitable candidates. Start with online directories, checking for reviews and ratings on sites like Yelp, Angie’s List, and HomeAdvisor. Then, ask friends, family, and neighbors for recommendations. Their firsthand experiences can be invaluable. Don’t hesitate to check with local building supply stores; they often have relationships with reliable contractors. Finally, consider contacting your local Better Business Bureau to check for any complaints filed against potential contractors. A combination of these approaches maximizes your chances of identifying qualified professionals.
Vetting Potential Contractors
Once you have a list of potential contractors, it’s time for thorough vetting. This involves checking licenses, insurance, and references. First, verify that the contractor holds the necessary licenses and permits required to operate legally in your area. Contact your local licensing board to confirm the validity and status of their license. Next, ensure they have adequate liability and workers’ compensation insurance. This protects you from financial liability in case of accidents or injuries on your property. Finally, request at least three references and contact them to inquire about the contractor’s work quality, professionalism, and adherence to timelines. Inquire about both positive and negative aspects of their experience.
Key Questions for Contractor Consultations
Before committing to a contractor, schedule consultations with your top choices. Asking the right questions during this phase is essential to assess their suitability for your project. Inquire about their experience with similar projects, their proposed approach to your specific siding needs, and their detailed breakdown of costs. Specifically ask about their warranty policies, their subcontracting practices (if any), and their project management process. Understand their communication methods and how they handle potential delays or unforeseen issues. Confirm their understanding of your vision and expectations for the project. Finally, request a written contract outlining all aspects of the agreement, including payment schedules and timelines. A well-defined contract protects both parties and ensures clarity throughout the process.
Budgeting and Financing Options
Source: shspros.com
Planning a new siding project requires careful budgeting to avoid unexpected expenses. A realistic budget accounts for not only the siding material itself but also labor, permits, potential repairs to underlying structure, and any unforeseen issues that may arise during the installation process. Failing to account for these hidden costs can lead to project delays and financial strain.
Creating a comprehensive budget involves several key steps. First, obtain multiple detailed estimates from reputable contractors. These estimates should itemize all costs, including materials, labor, and any additional fees. Compare these estimates carefully, looking for discrepancies and ensuring that all aspects of the project are included. Next, factor in a contingency buffer of 10-20% of the total estimated cost to cover unexpected expenses. This buffer can absorb the costs of unforeseen repairs, material price fluctuations, or other project hiccups. Finally, review your overall financial situation to determine how much you can comfortably afford to spend on the project without jeopardizing your financial stability.
Financing Options for Siding Projects
Several financing options exist to make a siding project more manageable. Home improvement loans are a common choice, offering a fixed interest rate and a set repayment schedule. These loans can be secured (using your home as collateral) or unsecured (not using your home as collateral), with secured loans typically offering lower interest rates. Another option is a home equity loan or line of credit (HELOC), which uses your home’s equity as collateral. HELOCs offer flexibility, allowing you to borrow and repay funds as needed, but they come with variable interest rates. Payment plans offered directly by contractors or through third-party financing companies can provide a more manageable payment schedule, often spread over several months or years. Each option has its pros and cons; careful consideration of interest rates, fees, and repayment terms is crucial before committing. For example, a 5-year loan at 7% interest on a $10,000 project will have significantly different monthly payments than a 10-year loan at the same interest rate.
Calculating Return on Investment (ROI) for New Siding
New siding can significantly increase your home’s curb appeal and market value, making it a worthwhile investment. Calculating the potential ROI involves comparing the cost of the project to the increase in your home’s value. For example, if you invest $15,000 in new siding and your home’s value increases by $20,000, your ROI is 33% (($20,000 – $15,000) / $15,000 * 100%). However, this is a simplified calculation. Factors such as the type of siding, the overall condition of your home, and the local real estate market can influence the actual return. A professional appraisal after the siding installation can provide a more accurate assessment of the increase in your home’s value. Additionally, energy-efficient siding can lead to lower energy bills, further enhancing the ROI by reducing ongoing costs. For instance, if energy-efficient siding reduces your annual heating and cooling costs by $500, this savings should also be factored into the overall ROI calculation over the lifetime of the siding.
Maintenance and Lifespan of Different Siding Types
Choosing the right siding for your home involves considering not only initial cost but also long-term maintenance and lifespan. Different materials age differently and require varying levels of upkeep, significantly impacting your overall homeownership costs. Understanding these factors will help you make an informed decision that aligns with your budget and lifestyle.
Expected Lifespan of Common Siding Materials, How much is new siding on a house
The lifespan of siding is heavily influenced by climate, installation quality, and maintenance practices. A harsh, sunny climate will naturally shorten the life of any siding compared to a milder one. Similarly, poor installation can lead to premature damage and reduced lifespan regardless of material. The following estimates provide a general guideline; actual lifespan may vary considerably.
Siding Material | Lifespan (Years) – Ideal Conditions | Lifespan (Years) – Harsh Conditions |
---|---|---|
Vinyl | 30-50 | 20-30 |
Fiber Cement | 50-80 | 30-50 |
Wood | 20-40 (with proper maintenance) | 10-20 (with proper maintenance) |
Aluminum | 40-60 | 30-40 |
Steel | 50-75 | 30-50 |
Note: “Harsh conditions” include prolonged exposure to extreme temperatures, high humidity, salt spray (near coastlines), and intense sunlight. Proper maintenance practices significantly extend the lifespan of all materials.
Routine Maintenance for Extended Siding Lifespan
Regular cleaning and inspection are crucial for preventing costly repairs and maximizing the lifespan of your siding. Neglecting maintenance can lead to problems like rot, insect infestation, and damage from moisture.
- Annual Cleaning: Use a garden hose and a soft-bristled brush to remove dirt, debris, and loose paint (if applicable). For stubborn stains, consider a pressure washer (low pressure setting) or a siding cleaner. Avoid harsh chemicals.
- Regular Inspections: Check for loose or damaged siding, signs of insect infestation, cracks, or water damage at least twice a year. Address any issues promptly to prevent escalation.
- Caulk Repairs: Regularly inspect and replace caulking around windows, doors, and other areas where siding meets other building materials. This prevents water intrusion.
- Paint or Stain (for wood siding): Wood siding requires periodic repainting or restaining to protect it from the elements. The frequency depends on the type of paint/stain and the climate. Consider using high-quality, exterior-grade products.
Costs Associated with Repairs and Replacements
Repair and replacement costs vary significantly depending on the type of siding, the extent of the damage, and the cost of labor in your area. Minor repairs, such as replacing a few damaged panels, might cost a few hundred dollars. However, extensive damage or complete siding replacement can cost thousands, even tens of thousands of dollars, depending on the size of the house and the chosen material.
For example, replacing a section of damaged vinyl siding might cost between $100 and $500, while replacing a large area of wood siding could easily exceed $5,000. Major repairs, such as repairing water damage behind the siding, will significantly add to the cost. It is always advisable to obtain multiple quotes from reputable contractors before undertaking any major repairs or replacements.
Final Summary
Replacing your home’s siding is a significant investment, but one that can dramatically improve your home’s curb appeal, energy efficiency, and overall value. By understanding the factors that influence the cost, carefully comparing different siding materials, and selecting a trustworthy contractor, you can ensure a smooth and successful project. Remember to factor in all associated costs, from materials and labor to permits and potential financing. With careful planning and the right information, you can confidently tackle this home improvement project and enjoy the beautiful, long-lasting results for years to come. Now that you have a better grasp on the costs involved, you’re well-equipped to start planning your siding upgrade.
Popular Questions
What’s the average lifespan of different siding types?
It varies greatly. Vinyl siding can last 20-40 years, wood siding 20-30 years (with proper maintenance), fiber cement 30-50 years, and metal siding 30-50 years or even longer.
Can I finance a new siding installation?
Yes, many financing options exist, including home improvement loans, credit cards, and payment plans offered by contractors. Shop around for the best rates and terms.
How do I find a reputable contractor?
Check online reviews, get multiple quotes, verify licenses and insurance, and ask for references. Don’t hesitate to ask detailed questions about their experience and process.
What are some hidden costs I should be aware of?
Permit fees, waste disposal, repairs to underlying sheathing, and unforeseen issues during installation can add to the overall cost. It’s wise to budget for contingencies.
How much does it cost to repair damaged siding?
Repair costs depend heavily on the extent of the damage and the type of siding. Minor repairs might be inexpensive, while extensive damage could require significant investment.
Comments are closed.