Replace Stucco with Hardie Board A Homeowners Guide
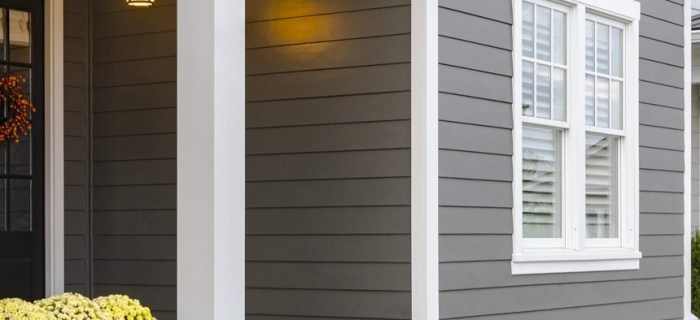
Replace stucco with Hardie Board: Thinking about upgrading your home’s exterior? This guide dives into the practical and aesthetic considerations of swapping out stucco for Hardie Board siding. We’ll compare costs, durability, looks, installation, and even the environmental impact to help you make an informed decision. Whether you’re tackling a small repair or a full-scale renovation, understanding the pros and cons of each material is key.
From initial material costs and labor estimates to long-term maintenance and aesthetic appeal, we’ll cover everything you need to know. We’ll explore the differences in durability and longevity, examining how each material holds up against various weather conditions and potential damage. We’ll also showcase the diverse design possibilities, showing how both stucco and Hardie Board can complement different architectural styles. Finally, we’ll walk you through the installation process, highlighting potential challenges and solutions.
Cost Comparison of Stucco and Hardie Board
Switching your home’s exterior from stucco to Hardie board is a big decision, and cost is a major factor. This section breaks down the expenses involved in both options, helping you make an informed choice. We’ll look at initial material costs, labor, and long-term maintenance, and provide a projected 20-year cost comparison.
Material Costs
The initial cost difference between the stucco and Hardie board is significant. Stucco, a cement-based mixture, is generally cheaper upfront. However, Hardie board, a fiber cement product, is more expensive per square foot due to its manufacturing process and superior durability. The price variation depends on factors like the stucco finish chosen (e.g., traditional, textured) and the specific type of Hardie board selected (e.g., panel, shingle). Expect to pay roughly $5-$15 per square foot for stucco and $10-$25 per square foot for Hardie board. These are broad ranges; getting accurate quotes from local suppliers is crucial for your specific project.
Labor Costs
Labor costs represent a substantial portion of the overall project expense. Stucco installation is labor-intensive, requiring skilled professionals to apply and finish the material correctly. This translates to a higher labor cost per square foot compared to Hardie board. Hardie board installation, while still requiring skilled labor, is generally faster and less intricate, potentially leading to lower labor costs overall. Expect to pay anywhere from $3-$8 per square foot for stucco installation and $4-$10 per square foot for Hardie board, again depending on location and complexity.
Long-Term Maintenance Costs
This is where the real difference between stucco and Hardie board shines. Stucco, while initially less expensive, is prone to cracking, water damage, and algae growth. Repairs can be costly and frequent. Regular repainting is also necessary, adding to the ongoing maintenance expense. Hardie board, on the other hand, is significantly more durable and resistant to these issues. While it might require repainting eventually, the frequency is much lower, resulting in substantially lower long-term maintenance costs. Consider the potential for costly repairs to stucco, which might include significant sections needing replacement, adding thousands of dollars to the overall cost over 20 years.
Twenty-Year Cost Comparison
The following table estimates the total cost of each option over 20 years for a hypothetical 1,000-square-foot home. These figures are estimates and can vary based on your location, material choices, and labor rates. Remember to obtain personalized quotes from contractors in your area.
Cost Category | Stucco | Hardie Board |
---|---|---|
Initial Material Cost | $7,500 – $15,000 | $10,000 – $25,000 |
Labor Cost | $3,000 – $8,000 | $4,000 – $10,000 |
20-Year Maintenance (Repairs & Repainting) | $10,000 – $20,000 | $2,000 – $5,000 |
Total Estimated 20-Year Cost | $20,500 – $43,000 | $16,000 – $40,000 |
Durability and Longevity: Replace Stucco With Hardie Board
Choosing between stucco and Hardie board often comes down to long-term performance. Both materials can last for decades, but their lifespans and resistance to various forms of damage differ significantly, making one a more suitable choice depending on your climate and budget. This section will delve into the specifics of each material’s durability and longevity.
Hardie board, a fiber cement siding, boasts superior durability compared to stucco. Its inherent strength resists impact damage far better than stucco, which is more prone to cracking and chipping from impacts, such as hail or accidental damage. This inherent strength translates to a longer lifespan with less maintenance.
Hardie Board’s Resistance to Damage
Hardie board’s resistance to damage extends beyond simple impact. Its composition makes it highly resistant to moisture damage, rot, and insect infestation. Unlike stucco, which can absorb water leading to cracking, mold growth, and structural weakening, Hardie board’s non-porous nature sheds water effectively. This inherent resistance minimizes the risk of costly repairs and replacements down the line. Furthermore, termites and other wood-boring insects pose little threat to Hardie board, unlike wood-based siding or stucco that might have wood components underneath.
Climatic Effects on Stucco and Hardie Board
Different climates present unique challenges to exterior building materials. Extreme heat can cause stucco to crack and peel, particularly if it wasn’t properly applied or if the underlying structure experiences expansion and contraction. Freezing temperatures can also damage stucco, leading to water expansion within the material and causing further cracking. High humidity can promote mold and mildew growth on stucco, requiring costly remediation.
Hardie board, on the other hand, performs well in a wider range of climates. While expansion and contraction can still occur, its fiber cement composition is less susceptible to cracking from temperature fluctuations. Its moisture resistance mitigates the risks associated with high humidity and freezing temperatures, significantly reducing the likelihood of mold and mildew.
Successful Hardie Board Installations in Diverse Climates
Hardie board has proven its durability in diverse climates across the globe. For instance, coastal regions with high humidity and salt spray, like the Gulf Coast of the United States, have seen numerous successful installations with minimal maintenance over decades. Similarly, areas with extreme temperature fluctuations, such as parts of the American Southwest and the Canadian Prairies, have demonstrated the material’s ability to withstand harsh conditions. Even in areas prone to hail, such as the Midwest, Hardie board’s impact resistance has proven beneficial, leading to reduced repair costs.
Problems with Stucco Addressed by Hardie Board
Stucco’s susceptibility to several issues makes it less desirable in many situations. Here are some key problems Hardie board effectively addresses:
- Cracking: Stucco is prone to cracking due to settling, temperature fluctuations, and impact damage. Hardie board’s inherent strength minimizes cracking.
- Water Damage: Stucco absorbs water, leading to mold, mildew, and structural damage. Hardie board’s non-porous nature prevents water absorption.
- Pest Infestation: Stucco can sometimes be vulnerable to pest infestations if wood components are present beneath. Hardie board is resistant to insect damage.
- High Maintenance: Stucco requires regular maintenance, including painting and repair, to maintain its appearance and structural integrity. Hardie board requires significantly less maintenance.
Aesthetic Considerations
Choosing between stucco and Hardie board often comes down to personal preference and the overall aesthetic you want to achieve for your home. Both materials offer a wide range of options, but their visual impact differs significantly, influencing the final look and feel of your house. Understanding these differences is crucial for making an informed decision.
Stucco and Hardie Board Visual Appeal by Architectural Style
Stucco, with its smooth or textured finish, lends itself well to Mediterranean, Spanish Colonial, and Southwestern architectural styles. Its ability to create seamless curves and intricate details makes it a popular choice for these designs. Hardie board, on the other hand, with its distinct plank or shingle appearance, complements more contemporary, craftsman, and farmhouse styles. The clean lines and varied profiles of the Hardie board create a modern or rustic aesthetic, depending on the chosen style. Traditional homes can also benefit from Hardie Board’s versatility, offering a classic look with a modern twist.
Color and Texture Options for Stucco and Hardie Board
Stucco offers a wide spectrum of color options, achieved through the addition of pigments to the mix. Textures range from smooth, almost plaster-like finishes to heavily textured surfaces that mimic natural stone or rough-hewn plaster. Hardie board provides a more limited palette of pre-finished colors, although custom painting is always an option. Textures vary depending on the board profile; you can find smooth, wood-grain, or even rough-sawn textures to emulate natural wood siding.
Example House Facades
Maintenance Comparison: Stucco vs. Hardie Board, Replace stucco with Hardie board.
Stucco requires periodic cleaning to remove dirt and grime. Larger cracks or damage may necessitate more extensive repairs, potentially requiring professional intervention. Regular inspections are important to identify and address minor issues before they escalate. Hardie board, being more resistant to moisture damage and insect infestation, generally requires less maintenance. Cleaning is typically straightforward, and minor repairs, such as replacing damaged panels, are often manageable for homeowners. However, repainting may be necessary every few years, depending on climate and sun exposure.
Installation Process
Source: sidingrepair.ca
Replacing stucco with Hardie board is a significant undertaking, requiring careful planning and execution. The installation process involves several key steps, from removing the old stucco to installing and finishing the new Hardie board siding. Understanding these steps is crucial for a successful and long-lasting result.
Stucco Removal
Removing existing stucco siding is a labor-intensive process that often requires specialized tools and expertise. Improper removal can damage the underlying structure, so it’s important to proceed cautiously. The process typically begins with assessing the stucco’s condition to determine the best removal method. Methods range from careful chipping and demolition hammers for smaller areas to using specialized equipment like a jackhammer for larger sections. Always protect yourself with appropriate safety gear, including eye protection, dust masks, and gloves.
- Assessment: Inspect the stucco for cracks, loose areas, and any signs of underlying damage. This will help determine the best removal method.
- Preparation: Protect surrounding areas with drop cloths or plastic sheeting to minimize dust and debris.
- Removal: Carefully remove the stucco using appropriate tools. For large areas, consider renting or hiring a professional demolition crew. Be mindful of the underlying sheathing and framing; avoid unnecessary damage.
- Disposal: Properly dispose of the removed stucco according to local regulations.
- Sheathing Inspection: Thoroughly inspect the underlying sheathing for any damage or rot. Repair or replace as needed.
Hardie Board Installation
Once the stucco is removed and the underlying structure is prepared, the Hardie board installation can begin. This involves several steps, from preparing the surface to finishing the seams and edges. Proper installation is critical for achieving a durable and aesthetically pleasing result.
- Preparation: Ensure the underlying sheathing is clean, dry, and structurally sound. Install any necessary weather barriers or vapor retarders.
- Cutting and Fitting: Measure and cut the Hardie board panels to fit the wall sections. Use a circular saw with a carbide-tipped blade specifically designed for fiber cement. Wear a respirator mask to avoid inhaling dust.
- Fastening: Secure the panels to the sheathing using galvanized nails or screws specifically designed forthe Hardie board. Follow the manufacturer’s recommendations for nail spacing and penetration depth. Avoid overdriving fasteners, which can cause cracking.
- Caulking: Apply a high-quality, paintable caulk to all seams and joints between panels. This helps create a weathertight seal and prevents water penetration.
- Finishing: Install trim pieces around windows, doors, and corners. Prime and paint the Hardie board to protect it from the elements and enhance its appearance. Allow adequate drying time between coats.
Installation Time Comparison
The time required for stucco removal and Hardie board installation varies significantly depending on the size of the project, the complexity of the existing stucco, and the experience of the installers. As a rough estimate, removing stucco might take 2-3 times longer than installing Hardie board for a comparable area. A small project (e.g., one side of a single-story house) might take a few days for stucco removal and a couple of days for Hardie board installation. Larger projects could easily take weeks or even months.
Potential Installation Challenges and Mitigation
Hardie board installation, while relatively straightforward, presents some potential challenges. Understanding these challenges and implementing appropriate mitigation strategies is key to a successful project.
- Moisture: Hardie board is susceptible to moisture damage. Properly managing moisture during and after installation is crucial. This includes using appropriate weather barriers and ensuring adequate ventilation.
- Cutting and Fitting: Precise cutting and fitting of panels are essential for a clean and professional look. Using a high-quality circular saw and taking accurate measurements are important. Consider using a jigsaw for intricate cuts.
- Fastener Placement: Improper fastener placement can lead to cracking or other damage. Following the manufacturer’s recommendations for nail spacing and penetration depth is crucial.
- Difficult Terrain: Working on uneven surfaces or around complex architectural details can make installation more challenging. Consider using specialized tools or techniques to overcome these challenges.
Environmental Impact
Source: bestexteriors.com
Choosing between stucco and Hardie board for your home’s exterior involves considering more than just aesthetics and cost; the environmental impact of each material is a crucial factor. Both options have environmental footprints, stemming from their manufacturing processes, transportation, and eventual disposal. Understanding these impacts helps make an informed, sustainable choice.
Manufacturing stucco involves mining and processing raw materials like cement, sand, and lime. Cement production, in particular, is energy-intensive and releases significant amounts of carbon dioxide, a major greenhouse gas. Hardie board, composed primarily of cement, cellulose fibers, and other additives, also has an environmental footprint associated with its manufacturing. However, the specific impact varies depending on the exact composition and manufacturing processes employed by different producers.
Manufacturing and Disposal
The environmental impact of manufacturing stucco is largely driven by the cement industry’s high energy consumption and CO2 emissions. Cement kilns require substantial fossil fuels to reach the necessary temperatures for the chemical reactions involved in cement production. Disposal of stucco, while generally inert, contributes to landfill volume. Hardie board’s manufacturing process, while also energy-intensive, generally results in a lower carbon footprint compared to stucco due to the use of cellulose fibers, a renewable resource. Disposal is similar, contributing to landfill space. However, some manufacturers offer recycling programs for their products, mitigating the landfill impact.
Sustainability and Recyclability
Stucco itself isn’t readily recyclable in the traditional sense. Once applied, it’s typically removed and disposed of as construction waste. Hardie board, while not widely recycled in many regions, offers better potential for reuse or recycling compared to stucco. Some manufacturers are actively working on developing improved recycling methods and increasing the use of recycled content in their products. This proactive approach indicates a growing focus on the sustainability of Hardie’s board.
Carbon Footprint
Precise carbon footprint calculations for stucco and Hardie board vary depending on factors such as the specific ingredients, manufacturing processes, and transportation distances. However, studies consistently show that the carbon footprint of cement-based products, including stucco, is generally higher than that of fiber cement products like Hardie board. This is primarily attributed to the energy-intensive nature of cement production. For example, a study by the Portland Cement Association (PCA) provides data on the carbon emissions per ton of cement, which can be used to estimate the overall carbon footprint of stucco projects. This data can be contrasted with the information provided by Hardie board manufacturers on their products’ environmental profiles.
Impact on Local Ecosystems
Both the stucco and Hardie board have potential impacts on local ecosystems, primarily during transportation and construction. Transportation of the materials contributes to air pollution and greenhouse gas emissions. Construction activities can lead to dust and noise pollution, impacting local air and noise quality. Moreover, the disposal of waste materials generated during installation and eventual demolition can contaminate soil and water resources if not properly managed. Implementing sustainable construction practices, such as minimizing waste and using environmentally friendly disposal methods, is crucial to mitigate these impacts for both materials.
Outcome Summary
Source: storables.com
Ultimately, the decision to replace stucco with Hardie Board depends on your individual needs and priorities. Weighing the factors discussed—cost, durability, aesthetics, installation, and environmental impact—will help you determine the best choice for your home. Remember to get multiple quotes from reputable contractors and thoroughly research the specific products you’re considering. With careful planning and execution, you can transform your home’s exterior into a beautiful and long-lasting investment.
Expert Answers
Can I install the Hardie Board myself?
While possible for smaller projects, professional installation is generally recommended for a quality, long-lasting result. It’s a more complex process than it might seem.
How long does Hardie Board siding last?
Hardie Board is known for its longevity, often lasting 30-50 years or more with proper maintenance.
Does Hardie Board require painting?
Yes, the Hardie Board needs to be primed and painted to protect it from the elements and maintain its appearance. Choose a paint specifically designed for fiber cement.
Is Hardie Board more resistant to pests than stucco?
Yes, Hardie Board is generally less susceptible to pest infestation compared to stucco, which can sometimes attract insects or rodents.
What about the warranty on Hardie Board?
Check the manufacturer’s warranty; it typically covers defects in materials and workmanship for a specified period.
Comments are closed.