What is the average cost of vinyl siding installed?
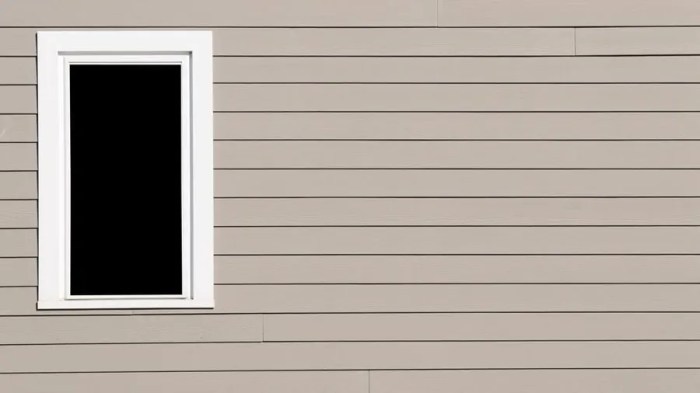
What is the average cost of vinyl siding installed? That’s a great question, and the answer isn’t a simple number. The price of a vinyl siding installation depends on a lot of factors, from the size of your house and the quality of the siding you choose to your location and the contractor you hire. We’ll break down all the major cost influencers so you can get a realistic estimate for your project. Think of it like building a LEGO castle – the more intricate the design and the fancier the bricks, the higher the cost.
This guide will walk you through the various elements that determine the total cost, from the raw materials and labor involved to regional price variations and potential hidden expenses. We’ll explore different siding types, quality levels, and installation methods, providing you with a comprehensive understanding of what to expect when budgeting for your new vinyl siding.
Factors Influencing Vinyl Siding Installation Costs: What Is The Average Cost Of Vinyl Siding Installed
Source: forbes.com
Getting vinyl siding installed can cost a pretty penny, and the final price tag depends on several key factors. Understanding these will help you budget effectively and avoid surprises. This section breaks down the major cost drivers.
House Size and Vinyl Siding Installation Costs
The size of your house is a major factor. More square footage means more siding needed and more labor hours, directly impacting the overall cost. For example, a 1,500-square-foot house will naturally require more siding and labor than a 1,000-square-foot house. Expect a roughly proportional increase in cost as the square footage increases. Always get quotes based on precise measurements of your home’s exterior.
Siding Quality and Price Variations
Vinyl siding comes in various grades, from standard to premium. Premium siding typically offers enhanced durability, thicker material, more color options, and potentially better warranties. While standard siding might seem cheaper upfront, it might not last as long, potentially costing more in the long run due to earlier replacement needs. The price difference per square foot can be significant, sometimes doubling or even tripling between the cheapest and most expensive options. Consider the long-term value when making your selection.
Installation Method Cost Differences
Different installation methods can also affect the price. A more complex installation, such as one requiring extra work around intricate architectural details or difficult-to-access areas, will generally cost more. Simpler, straightforward installations on a regularly shaped house will be less expensive. The installer’s experience and expertise also play a role; experienced installers may charge a premium but deliver a higher quality, faster installation.
Labor Costs Across Geographical Locations
Labor costs vary significantly depending on your location. Areas with higher costs of living generally have higher labor rates for contractors. For instance, a siding installation in a major metropolitan area like New York City will likely be more expensive than in a smaller town in the Midwest. This is due to factors such as higher demand, competition, and the general cost of living in that region. Get multiple quotes from local installers to compare labor rates.
Additional Costs: Permits and Material Disposal
Beyond the cost of materials and labor, you should budget for additional expenses. Permits are often required for exterior home renovations, and their cost varies by location and project scope. Proper disposal of old siding and construction debris is also an important consideration; most contractors include this in their quote, but it’s worth clarifying upfront to avoid unexpected charges. These hidden costs can add up, so it’s best to be prepared.
Cost Comparison of Different Siding Types
Siding Type | Price per Square Foot (Low End) | Price per Square Foot (Mid-Range) | Price per Square Foot (High End) |
---|---|---|---|
Standard Vinyl | $3-$5 | $6-$8 | $9-$12 |
Premium Vinyl | $6-$9 | $10-$15 | $16-$25+ |
Insulated Vinyl | $8-$12 | $14-$20 | $22-$35+ |
Vinyl Shake/Shingle | $7-$10 | $12-$18 | $19-$30+ |
Material Costs Breakdown for Vinyl Siding Installation
Source: homeimprovementcents.com
Understanding the material costs is crucial for budgeting your vinyl siding project. Prices vary significantly based on several factors, including brand, color, texture, thickness, and the need for additional components like trim and accessories. This breakdown will help you navigate these complexities.
Vinyl Siding Brand Prices
Different manufacturers offer vinyl siding at varying price points. Generally, you’ll find a range from budget-friendly options costing around $1 to $3 per square foot to premium brands reaching $5 or more per square foot. The price difference often reflects the quality of the materials, the warranty offered, and the features included, such as enhanced durability or impact resistance. For example, a well-known, high-end brand might offer a longer warranty and superior fade resistance, justifying the higher price tag. Conversely, more economical brands might offer a shorter warranty but still provide acceptable performance for a budget-conscious homeowner.
Vinyl Siding Color and Texture Costs
While the base price of vinyl siding is determined by the brand and thickness, the color and texture can add to the overall cost. Solid colors are typically the least expensive. More complex colors, such as those with flecks or wood grain patterns, might cost slightly more. Similarly, textured siding, designed to mimic wood shake or other materials, tends to be priced higher than smooth siding. The increased cost is often due to the added manufacturing complexity required to create the texture. For instance, a “cedar shake” texture will generally be more expensive than a smooth, solid white option.
Costs of Trim, Flashing, and Fasteners
Beyond the siding itself, you’ll need trim pieces, flashing, and fasteners to complete the installation. Trim pieces, used around windows, doors, and corners, can add 10-20% to the total material cost. Flashing, crucial for water protection, is also essential and adds to the expense. Fasteners, such as nails or screws, represent a smaller but necessary expense. The specific cost of these items will vary based on the quantity needed and the type of material used. For example, higher-quality, corrosion-resistant fasteners will cost more than standard nails.
Cost of Common Accessories
It’s important to factor in the cost of accessories such as soffit and fascia boards. These components complete the look and protect the underside of your roofline.
- Soffit: Prices typically range from $1 to $5 per linear foot, depending on material and style.
- Fascia: Similar to soffit, fascia costs usually range from $1 to $5 per linear foot, with variations based on material and style.
- J-Channel: Used for finishing edges, this typically costs between $0.50 and $2.00 per linear foot.
- Corner Trim: Expect to pay between $1 and $4 per linear foot.
The overall cost of these accessories will depend on the size of your house and the complexity of the design.
Vinyl Siding Thickness Costs
Vinyl siding comes in various thicknesses, typically measured in inches. Thicker siding generally offers greater durability and resistance to impact damage. A thicker panel (e.g., .046 inch) will generally cost more per square foot than a thinner panel (e.g., .040 inch). While the difference might seem small, it can add up to a large project. The added cost is justified by the enhanced longevity and resilience to harsh weather conditions. For example, in areas with frequent hailstorms, investing in thicker siding could prove to be a cost-effective measure in the long run.
Labor Costs and Contractor Selection
Choosing the right contractor significantly impacts the final cost of your vinyl siding installation. Labor represents a substantial portion of the overall expense, and understanding the factors influencing these costs is crucial for budgeting and project planning. This section will break down labor costs, contractor choices, and potential hidden expenses.
Hourly Rates of Experienced Vinyl Siding Installers
Experienced vinyl siding installers typically charge hourly rates ranging from $40 to $80, depending on factors such as location, experience, and demand. Highly skilled installers with a proven track record and specialized skills, such as intricate trim work, often command higher rates at the upper end of this range. These rates are usually inclusive of the cost of labor only; materials are billed separately. Regional variations significantly affect hourly rates, as discussed in the table below.
Cost Comparison: Single Contractor vs. Larger Company
Hiring a single contractor often results in lower overhead costs passed on to the homeowner, potentially leading to slightly lower overall labor charges. However, larger companies may offer benefits like more comprehensive insurance coverage, greater access to resources and materials, and potentially more streamlined project management. The choice depends on individual project needs and preferences. For smaller projects, a single contractor might be more cost-effective, while larger, more complex projects could benefit from the resources a larger company provides.
Hidden Costs During Vinyl Siding Installation, What is the average cost of vinyl siding installed
Several unexpected costs can arise during a vinyl siding installation. These hidden costs can include unforeseen repair work to underlying sheathing or framing, the need for additional materials due to inaccurate measurements or damage, permit fees, and disposal fees for old siding and debris. For instance, discovering extensive rot beneath the old siding requires additional labor and material costs to repair before new siding can be installed. Accurate pre-installation assessment helps minimize these surprises.
Labor Costs Associated with Old Siding Removal
Removing existing siding adds to the overall labor cost. The complexity of removal depends on the type of siding being removed (e.g., wood, aluminum, asbestos) and its condition. Removing old wood siding, which often involves nails and potential damage to the underlying sheathing, is typically more expensive and time-consuming than removing vinyl siding. Expect to pay an additional $1 to $3 per square foot for old siding removal, on top of the new siding installation cost.
Impact of Project Complexity on Labor Expenses
Intricate designs, such as complex trim work, multiple colors, or unusual architectural features, significantly increase labor costs. These details require more time, skill, and precision, leading to higher hourly rates or a longer overall project timeline. For example, a house with many dormers or bay windows will likely demand more labor hours compared to a simple rectangular structure.
Regional Hourly Rates for Vinyl Siding Installers
Region | Hourly Rate Range |
---|---|
Northeast US | $50 – $80 |
Southeast US | $40 – $65 |
Midwest US | $45 – $70 |
Southwest US | $45 – $75 |
West Coast US | $60 – $90 |
Regional Variations in Vinyl Siding Installation Costs
Source: premierroofsct.com
Vinyl siding installation costs aren’t uniform across the United States. Several factors contribute to significant price differences between states and even within smaller geographic areas. Understanding these variations is crucial for accurate budgeting and realistic expectations.
Average Installation Costs Across Different US States
The average cost of vinyl siding installation can vary widely depending on location. For example, states with a higher cost of living, such as California or New York, typically see higher installation costs compared to states in the Midwest or South. This difference isn’t solely due to material prices but also reflects variations in labor rates, permitting fees, and the overall competitive landscape of the construction industry in each region. A rough estimate might put California’s average cost higher by 20-30% compared to a state like Iowa, even if the same type and quality of siding is used. These figures are broad generalizations; specific costs will depend on project size and complexity.
Local Market Conditions and Their Impact on Overall Cost
Local market conditions significantly influence vinyl siding installation prices. Areas experiencing a construction boom often have higher labor costs due to increased demand for skilled workers. Conversely, regions with slower economic growth might offer more competitive pricing. The availability of local contractors also plays a role; a highly competitive market with many contractors will usually lead to lower prices, while areas with limited contractors may result in higher prices due to reduced competition. For example, a rapidly growing suburban area might experience a 15-20% price increase compared to a similar-sized town in a slower-growing region.
Permit Fees and Their Regional Variations
Permitting fees for home improvement projects, including vinyl siding installation, vary substantially from region to region. Some localities have higher permit fees due to stricter regulations or more extensive review processes. These fees are typically based on the project’s estimated cost, with higher-cost projects incurring higher fees. In some areas, the permit fee might be a flat rate, while others use a percentage-based system. A project costing $10,000 in one area might incur a $200 permit fee, while the same project in another area might only cost $50 or as much as $500.
Local Labor Costs and Their Influence on Final Installation Price
Labor costs represent a significant portion of the overall vinyl siding installation price. Areas with higher minimum wages or a strong union presence tend to have higher labor costs. The skill level and experience of the installers also influence the price. Highly skilled and experienced installers often charge more than less experienced ones. This variation can easily account for a 10-20% difference in the final installation cost between regions with different labor market dynamics. For example, a coastal city with a high cost of living will likely have higher labor costs than a smaller inland town.
Factors Contributing to Higher Costs in Specific Geographic Areas
Several factors can contribute to higher vinyl siding installation costs in certain geographic areas. These include: high material transportation costs due to remoteness or difficult terrain; a limited supply of local contractors; stringent local building codes and regulations leading to higher permitting fees and inspection costs; and a higher prevalence of specialized labor requirements due to unique local climate conditions or building styles. For instance, a mountainous region might experience significantly higher transportation costs for materials, directly impacting the overall project cost.
Visual Aids
Source: powellsroofing.com
Visual aids can significantly improve understanding when dealing with complex topics like vinyl siding installation costs. Clear visuals help homeowners grasp the cost breakdown and make informed decisions. We’ll explore two helpful visual representations.
Illustrating Cost Breakdown on a House Diagram
Imagine a simple diagram of a house, drawn to scale. Different sections of the house’s exterior – the front, sides, and back – are delineated. Each section is assigned a different color, corresponding to a specific cost per square foot. For example, the front might be a darker shade of blue, reflecting a higher cost due to more intricate detailing or larger windows that require extra work. The sides, perhaps a lighter blue, would represent a lower cost per square foot due to the simpler design. The back, shown in a pale blue, could represent the lowest cost area. Numbers representing the square footage of each section and the calculated cost per area are clearly labeled. The total cost is prominently displayed. This allows a homeowner to visually see how the different areas contribute to the overall expense. The differences in cost per square foot between areas could be explained in a legend, indicating factors such as the complexity of the design, the presence of windows or doors, or the need for extra materials. A simple calculation, like cost per square foot multiplied by the area, is shown for each section to make the calculation process transparent. For example, if the front is 200 square feet at $8 per square foot, it would be marked as costing $1600.
Comparing Siding Material Costs and Durability
A bar chart would effectively compare different siding materials. Each bar represents a type of siding (e.g., vinyl, wood, fiber cement, aluminum). The height of the bar represents the cost per square foot. To show durability, a color gradient could be used within each bar. A darker shade of the bar’s color (e.g., a darker blue for vinyl) could represent high durability, while a lighter shade (a lighter blue for vinyl) could show lower durability. A key explaining the color gradient scale (e.g., dark blue = highest durability, light blue = lowest durability) would be included. This allows for a direct visual comparison of both cost and durability, helping homeowners weigh the trade-offs between upfront cost and long-term value. For instance, a fiber cement siding bar might be taller than a vinyl siding bar, reflecting its higher initial cost, but the color gradient would show a darker shade, illustrating its superior durability and longevity.
Final Summary
So, while there’s no single answer to “What is the average cost of vinyl siding installed?”, understanding the contributing factors—house size, siding quality, labor costs, and regional differences—is key to getting an accurate estimate. By carefully considering these elements and comparing quotes from reputable contractors, you can confidently plan and budget for your vinyl siding project. Remember to factor in potential extras and always get everything in writing before starting the work. Happy siding!
Question & Answer Hub
What’s the warranty typically offered on vinyl siding?
Vinyl siding warranties vary by manufacturer, but typically range from 20 to 50 years, covering defects in materials and workmanship.
Can I install vinyl siding myself?
While possible, DIY vinyl siding installation is generally not recommended unless you have significant experience with home improvement projects. Professional installation ensures a proper and long-lasting result.
How long does vinyl siding installation usually take?
The installation time depends on the size of the house and the complexity of the project, but it can range from a few days to several weeks.
What are some signs of a bad vinyl siding installation?
Look for uneven gaps between panels, poorly cut edges, damage to the siding, or improper flashing around windows and doors.
How often should I clean my vinyl siding?
Regular cleaning, typically once or twice a year, with a garden hose and a soft brush helps maintain its appearance and prolong its lifespan.
Comments are closed.